In the ValorPlast project researchers at the University of Natural Resources and Life Sciences‘ Institute for Environmental Biotechnology are investigating how to transform sugar-industry byproducts into biopolymers. The project consortium includes Bioenergy 2020+ GmbH, Agrana Research & Innovation Center GmbH, IM Polymer GmbH and the Institute for Chemistry and Technology of Materials at Graz University of Technology.
By developing novel processing methods for sugar biorefineries, the researchers aim to make more efficient use of the raw material sugar beet and open up new applications, so as to make the industry more competitive. Up to now utilizing residues from the sugar industry was focussed almost entirely on molasses. For desugarized (residual) molasses and beet pulp the only options were the utilization as animal feed, as fertilizer or as a source of energy.
Making biopolymers
As part of ValorPlast residual molasses and beet pulp are to be fermented to yield PHAs (polyhydroxyalkanoates). These bio-based, biodegradable polymers have been identified as the most suitable product that can be obtained from transforming the residues by biotechnological means. PHAs can be used as packaging material, as compostable single-use products or in biomedical engineering, for instance. Up to now market opportunities have been limited by price, since the main feedstocks for making PHAs were refined sugars.
Two novel fermentation processes are being investigated in the project. One uses residual molasses as feedstock. Because this byproduct has a high salt content, there are currently no high-grade uses for it. However, its salt content can be an advantage in the fermentation process, because it is possible to employ halophilic (salt-loving) microorganisms that allow cultivation at non-sterile conditions. Some of these halophilic microorganisms can produce short-chain-length (scl) PHAs. The second process is meant to transform beet pulp into medium-chain-length (mcl) PHAs; these polymers are more elastic and have different processing characteristics which open up new areas of application for PHAs. In a two-stage process the beet pulp is pre-acidified to form volatile fatty acids, which are then transformed into PHAs.
Test specimens of PHA are made from the fermentation products and their processing and application characteristics are investigated. Finally the processes are evaluated overall; this involves assessing their potential and carrying out detailed economic analysis.
Initial findings
In the first year of the project the focus was on characterizing the feedstocks and on analysing and improving the acidification process for beet pulp at laboratory scale. The compositions of differing feedstocks (residual molasses and beet pulp) are already known and can be used for planning fermentation experiments. The acidification process for beet pulp has already been developed, with the most important process parameters defined. Preparations are currently in progress for moving on to a continuous process.
Various strains of microorganism that may be suitable for producing PHAs from the feedstocks selected have been investigated. One of the salt-tolerant strains identified is particularly promising, because residual molasses can be used at a relatively high concentration and PHA contents of up to 50 % of the dry matter in the biomass were obtained in the first experiments. Microorganisms suitable for producing mcl PHA have also been identified, with a view to improving the process further.
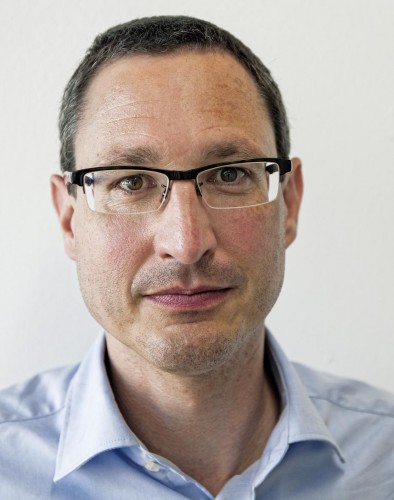
Markus Neureiter
University of Natural Resources and Life Sciences, Vienna
Department IFA-Tulln, Institute for Environmental Biotechnology
Share