To enable the efficient and sustainable energy supply of industrial manufacturing, both the demand of individual processes and the availability of thermal and electric energy must be aligned. Industrial companies need tools and methodologies for designing and optimising their energy supply systems, particularly with a view to integrating a high percentage of renewable energy. Industrial energy supply is currently largely set up to use a handful of supply technologies and cannot respond in the best possible way to fluctuating, process-driven demand or the volatile availability of renewable energy.
Modelling energy-related processes
A concept and suitable software tool for optimising the design and operation of industrial energy supply systems is being developed as part of the Digital Energy Twin1 lead project, which is being led by AEE – Institute for Sustainable Technologies (AEE INTEC). It is employing a method known as a digital twin, which was previously used mainly to optimise production workflows and logistical issues in industry. The digital twin enables detailed models of selected energy-related processes and renewable energy supply technologies to be developed, validated and simplified for the first time.
Optimisation based on live operating data
The main purpose of the project is to develop a holistic optimisation algorithm based both on operating and process data from standardised examples and on real-life manufacturing industry operating data from the printed circuit board manufacturer AT&S. This company will be applying the new tools that are being developed with the vision to extend the Digital Energy Twin to the whole system at AT&S in Hinterberg/Leoben and finally all production sites worldwide. The Digital Energy Twin offers a solution for the need to balance fluctuating energy demand at process level, a volatile supply of renewable energy and the use of process and supply technologies that are as efficient as possible.The digital twin method can also be combined with augmented and virtual reality (AR/VR), two technologies that could be used to monitor and control production and energy systems efficiently in the future.
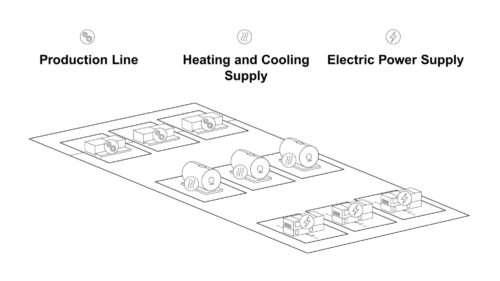
Low-cost application
The project is developing standardised models for energy-related process and supply technologies, thus ensuring that the method can be reproduced and applied at low cost in many other industry sectors. This optimisation method will help companies to better gauge and reduce the risks involved in investing in sustainable energy systems. The project is thus making a key contribution to broadening the scope for using energy-efficient process and supply technologies and integrating renewable energy sources in industrial manufacturing.
Project goals
> Developing a holistic optimisation algorithm for industrial energy systems
> Developing and validating the Digital Energy Twin tool and methodology
> Enabling holistic modelling of the industrial energy system including both conventional and renewable technologies
> Validating data security and data management between software and hardware components
> Devising a standardised model to make Digital Energy Twin transferable
> Incorporating augmented and virtual reality for human-machine interaction as part of the Fourth Industrial Revolution
https://energieforschung.at/projekt/optimised-operation-and-design-of-industrial-energy-systems/
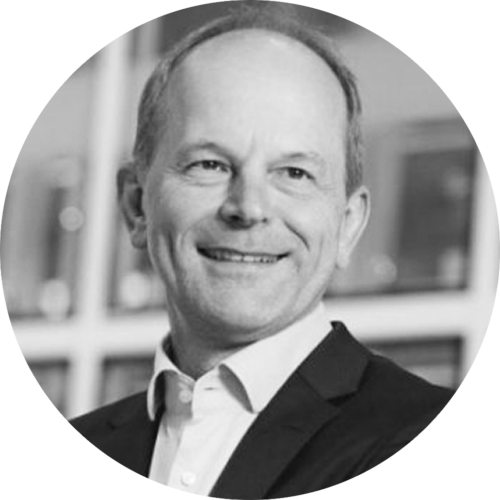
„To make our circuit boards, we at AT&S use highly specialised facilities and processes that also need a complex energy system. All manufacturing steps and the associated processes are monitored very closely and optimised continuously so that we can make our production efficient, sustainable and high quality. This also means embracing innovative solutions: having a Digital Energy Twin of one of our manufacturing facilities lets us identify further opportunities for optimisation along the production and energy supply chain and make the most of them. This is increasing flexibility and efficiency in our production further while also going a long way towards making circuit board manufacture even more environmentally and resource-friendly.“
Andreas Gerstenmayer
CEO of AT&S
1 Project partners: AEE INTEC (project management), AT&S Austria Technologie & Systemtechnik Aktiengesellschaft, FH Vorarlberg University of Applied Sciences: Research Center Digital Factory Vorarlberg / Research Center Energy / Research Center User Centered Technologies / VR Lab, FH Salzburg University of Applied Sciences / Information Technology & System Management, Graz University of Technology / Institute for Software Technologies / Institute for Interactive Systems and Data Science, University of Leoben / Chair of Energy Network Technology, Eberle Automatische Systeme GmbH & Co KG, Enertec Naftz & Partner GmbH & Co KG, Schmoll Maschinen GmbH, VTU Energy GmbH Bravestone Information-Technology GmbH
Share