Bei der Roheisengewinnung im Hochofenprozess entsteht pro Tonne Roheisen als Nebenprodukt ca. 300 kg heiße, flüssige Schlacke, die im Wesentlichen aus CaO und SiO2 (Calciumoxid und Siliziumdioxid) sowie Al2O3 und MgO (Aluminium- und Magnesiumoxid) besteht. Weltweit werden jährlich etwa 400 Mio. Tonnen Hochofenschlacke mit bis zu 1.500°C erzeugt. Je nachdem wie schnell die Schlacke abgekühlt wird, weist sie unterschiedliche mineralische Eigenschaften auf. Bei langsamer Abkühlung an Luft entsteht kristalline Hochofenstückschlacke, beim schnellen Abkühlen im Wasser glasiger Hüttensand. Gemahlener Hütten-sand wird überwiegend in der Zementindustrie als Bestandteil von sogenannten Portlandhütten- und Hochofenzementen verwendet.
Das gängige Verfahren zur Gewinnung von Hüttensand ist die Nassgranulation. Das energetische Potenzial der Hochofenschlacke von ca. 1,8 GJ pro Tonne Schlacke bleibt in diesem Verfahren ungenutzt.
Innovative Technologie
Im Rahmen von FORWÄRTS und dem Folgeprojekt FORWÄRTS 2.0 wird ein neuartiges Konzept von Primetals Technologies Austria GmbH für die trockene Granulation von Hochofenschlacke in einer Pilotanlage umgesetzt. Dieses innovative Verfahren ermöglicht es, die an die Luft abgegebene Wärme mittels Wärmerückgewinnung für weitere Prozesse zu nutzen. So sollen Energie und Wasser eingespart werden. Neben der voestalpine Stahl GmbH wirken die Montanuniversität Leoben/Lehrstuhl Thermoprozesstechnik und FEhS – Institut für Baustoff-Forschung e.V. an der Umsetzung am Hochofen der voestalpine am Standort Linz mit. Derzeit befindet sich die Anlage in der Inbetriebnahmephase.
Die Anlage arbeitet nach dem sogenannten „Rotating Cup“-Prinzip. Dabei wird die flüssige Schlacke auf einen schnell rotierenden Drehteller aufgebracht. Durch die auftretenden Kräfte wird die Schlacke in feine Tropfen zerrissen und radial an eine wassergekühlte Wand geschleudert. Auf dem Millisekunden dauernden Flug werden diese Partikel mit Luft gekühlt, die heiße Abluft wird abgeführt. Ziel in dieser Projektphase ist es, hochqualitativen Hüttensand herzustellen. Wichtigstes Merkmal für die Qualität des Hüttensands ist der Glasgehalt, der über 95 % liegen soll und eine wesentliche Einflussgröße für die latent-hydraulische Reaktion des Hüttensands darstellt. Diese Reaktion beeinflusst die Festigkeit der damit hergestellten Zemente und Betone.
Bei einem erfolgreichen Abschluss der jetzigen Projektphase, mit der Bestätigung des anlagentechnischen Konzepts und der Qualität des Hüttensandes kann in weiterer Folge ein Gesamtkonzept inklusive Wärmerückgewinnung im industriellen Maßstab erstellt werden. Für das Konzept der nachgeschalteten Wärmerückgewinnung könnte ab dem Jahr 2019 ein weiteres Forschungsprojekt folgen. Die zurückgewonnene thermische Energie der Schlacke kann z. B. für die Produktion von Prozessdampf und/oder Strom verwendet werden oder für verschiedene andere Vorwärm- oder Heizzwecke zum Einsatz kommen.
Ressourcen einsparen
Mit dem neu entwickelten Verfahren zur Trockenschlackegranulation können Wassereinsparungen von bis zu 95 % erzielt werden. Außerdem wird keine Energie für die Trocknung des Hüttensands benötigt. Bei der Nassgranulation liegt der Energiebedarf für die Nachtrocknung bei rund 130 kWh pro Tonne. Gegenüber dem Stand der Technik wären daher weltweit jährlich Einsparungen von rund 280 PJ thermischer Energie möglich. Mit der Option der elektrischen Energierückgewinnung entspricht dies einem weltweiten CO2-Einsparungspotential von 17 Mio. Tonnen pro Jahr.
Demonstration und Evaluierung
In der Pilotanlage am Standort der voestalpine in Linz wird der Prozess unter realen Bedingungen im Hüttenwerk getestet, optimiert und weiterentwickelt. Seit Juni 2017 werden nach jedem Versuchslauf detaillierte Auswertungen zur Prozessentwicklung durchgeführt, die in die anlagentechnische Optimierung einfließen. Im Fokus stehen u. a. die Prozessabläufe am Drehteller, die Prozessabluft, die Wirbelschicht und die Produktqualität. Erste Analysen des Glasgehaltes des Hüttensands zeigen positive Resultate und liegen über dem angestrebten Ziel.
Um das Forschungsziel eines automatisierten Betriebs unter Einhaltung der geforderten Produktanforderungen zu gewährleisten, werden geeignete Mess-, Steuer- und Regelungssysteme für die Rotationzerstäubung der flüssigen Hochofenschlacke benötigt. Basierend auf den bereits gesammelten Erkenntnissen werden bei den Forschungspartnern Grundlagenuntersuchungen durchgeführt, die an der Pilotanlage verifiziert werden.
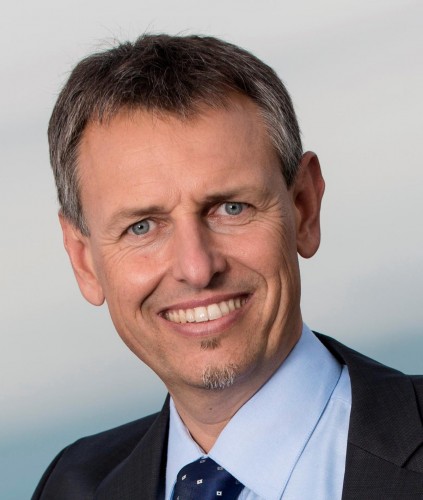
„Die Verwertung der Schlacke aus der Roheisenerzeugung mit gleichzeitiger Nutzung des Wärmeinhaltes ist ein global noch ungelöstes Thema mit hohem Potenzial. Primetals Technologies hat sich zusammen mit seinen Entwicklungspartnern die Aufgabe gesetzt, ein Verfahren zur Trockenschlackengranulation mit möglichst hoher energetischer Verwertung des Wärmeinhalts der Schlacken zur industriellen Reife zu entwickeln. Dieses Vorhaben ist eines der größten und bedeutendsten Forschungsprojekte bei Primetals Technologies. Das DSG1 Verfahren birgt ein enormes Potenzial zur Erhöhung der Energieeffizienz in der Eisen- und Stahlerzeugenden Industrie. Unter der Annahme, dass die Hälfte der Hochöfen global dieses Verfahren einsetzt, entspricht dies der Energiemenge von etwa 3,5 Mio. Haushalten oder 6,5 Mio. E-PKW bei 10.000 km jährlicher Leistung.“
DI Dr. Alexander Fleischanderl
Technology Officer Up-Stream, Vice President Iron & Steelmaking and Head of ECO Solutions, Primetals Technologies Austria
1 DSG = Dry Slag Granulation/Trockenschlackegranulation
Share